Hydrogenation with Metal Complexes and Chiral Ligands
Mechanism + Description
For synthesis, the principal enzyme class is the Enoate or Ene reductases. These enzymes can reduce activated alkenes in a stereospecific anti fashion by the delivery of hydride from a reduced FMN co-factor followed by protonation. The oxidized FMN co-factor is regenerated by NADPH, so the reaction needs to be driven by the NADPH – NADP+ cycle.
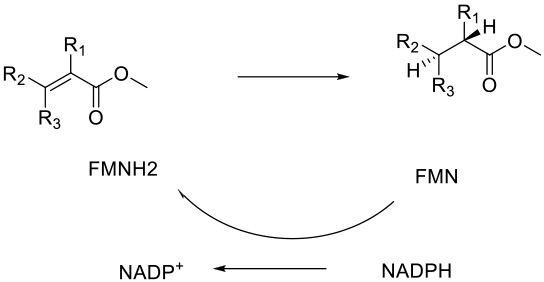
General comments
It has been known for some time that ‘old yellow enzymes’ in yeasts will reduce activated alkenes to give chiral products. Recently, OYE-type enzymes have been the subject of a great deal of study, and many ene reductases can now be used as isolated enzymes rather than as whole-cell biocatalysts. The alkene needs activation with a(n) electron-withdrawing group(s) to stabilize the anion formed after the hydride addition. The current range of substrates that can be reduced with ene reductases is limited, but is constantly being expanded as new enzymes are developed.
Key references
Relevant Scale-Up Examples with Scheme
ChemCatChem. 2015, 7 (8), 1302 – 1311.
Experimental
300 mg scale
Specific solvent issues with chiral hydrogenation of C=C bonds
Asymmetric hydrogenations have been carried out in a wide range of solvents – preferred are lower mol wt alcohols, simple esters, and greener ethers like 2-MeTHF.
Chlorinated solvents like dichloromethane( DCM), 1,2-dichloroethane and CHCl3 should be avoided if at all possible.
With very high S/C rations, a solvent’s quality needs careful consideration as even very small amounts of certain impurities can inhibit the catalyst.
Likewise, care should be used when using recycled solvents since low levels of impurities and oxidation products that may not be apparent on the specification may inhibit the catalyst.
Water is not a common solvent for the asymmetric hydrogenation of alkenes, but there are reports of immobilized/ water-soluble catalysts.