Hydrogenolysis
Mechanism + Description
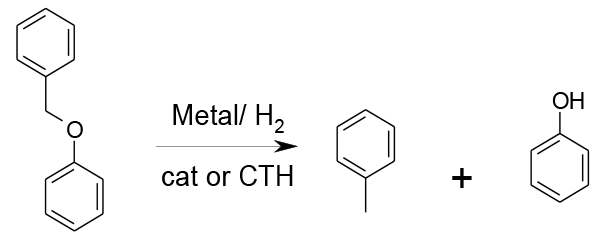
Bonding of the substrate and hydrogen to active sites on the metal leads to cleavage of the ether and generation of the phenol or acid and toluene or other hydrocarbon. Transformations are catalytic or Catalytic Transfer Hydrogenation (CTH).
General comments
Typically used to cleave benzyl and related ethers and esters. A wide range of metals have been employed as catalysts and both gas and transfer hydrogenation reactions can be used (see references and experimental examples).
Usually hydrogenolysis of benzyl ethers and esters takes place under mild conditions and temperature. Care needs to be taken with catalyst selection to ensure compatibility with other reducible functional groups. Most catalysts employed are heterogeneous and thus easily recovered. However, levels of metal leached into the reaction waste streams or taken through with the product need to be determined.
Recent advances in catalytic technology relating to processing bio-renewable feedstocks has shown the ethers other than benzyl can be cleaved by hydrogenolysis. Nickel complexes have also been reported to be active, although the major goal of this research area so far has been in deoxygenation rather than dealkylation. Nevertheless, alcohols have been reported as products and thus it maybe possible to fine tune reactivity to make hydrogenolysis an option for cleaving simple methyl, ethyl ethers.
Key references
Green Chemistry, 2002, 4, 492 Mild catalytic multiphase hydrogenolysis of benzyl ethers
Science, 2011, 332, 439 Selective, Nickel-Catalyzed Hydrogenolysis of Aryl Ethers
J. Am . Chem. Soc., 2012, 134, 20226 A Heterogeneous Nickel Catalyst for the Hydrogenolysis of Aryl Ethers without Arene Hydrogenation
Org. Process Res. Dev. 2004, 8, 101 – H2/Pd-C
Relevant scale up example (see also ester deprotection guide for hydrogenolysis of benzyl esters)
Experimental
5 Kg scale
Org. Process Res. Dev., 2008, 12, 414
Experimental
5 Kg scale
Org. Process Res. Dev.,2008, 12, 1170
Experimental
5 Kg scale
Org. Process Res. Dev., 2005, 9, 314
Experimental
7 Kg scale
Org. Process Res. Dev., 2013, 17, 658
Green Review
-
Atom efficiency (by-products Mwt)
With optimized catalytic efficiency, hydrogenolysis is an atom efficient process. - Safety Concerns
Typified by normal hazards around hydrogenation reactions. Catalytic transfer hydrogenation (CTH) may avoid the need to handle H2 gas. - Toxicity and environmental/aquatic impact
Main concern is around solubilisation and loss of precious metal/ heavy metal (PM/HM) catalysts into waste streams. Most PM/HM levels are tightly regulated. The same applies to potential carry through into the API- see next slide. Some Ni salts are sensitizers and carcinogens and listed on the EU SVHC (substances of Very High Concern) list – this is of less concern for metallic hydrogenation catalysts. - Cost, availability & sustainable feedstocks
H2 obtained via CTH is cheap and non-polluting and has the potential to be made from renewable resources. - Sustainable implications
All metals have a high LCI impact from mining and refining operations, so use should be catalytic with efficient recovery and recycle. Pd is most commonly used precious metal for hydrogenolysis and this is rated at high risk of depletion. No concern for abundant base metals like Ni.
ICH guide line on metals in API (2014)
Classification | Oral Exposure | Parenteral Exposure | Inhalation exposure* | ||
PDE (μg/day) |
Concentration (ppm) |
PDE (μg/day) |
Concentration (ppm) |
PDE (ng/day) |
|
Class 1A: Pt, Pd Class 1B: Ir, Rh, Ru, Os Class 1C: Mo, Ni, Cr, V Metals of significant safety concern |
100 100** 250 |
10 10** 25 |
10 10** 25 |
1 1** 2.5 |
Pt: 70* Ni: 100 Cr(VI): 10 |
Class 2: Cu, Mn Metals with low safety concern |
2500 | 250 | 250 | 25 | |
Class 3: Fe, Zu Metals with minimal safety concern |
13000 | 1300 | 1300 | 130 |