Arene/Heteroarene Saturation
Mechanism + Description
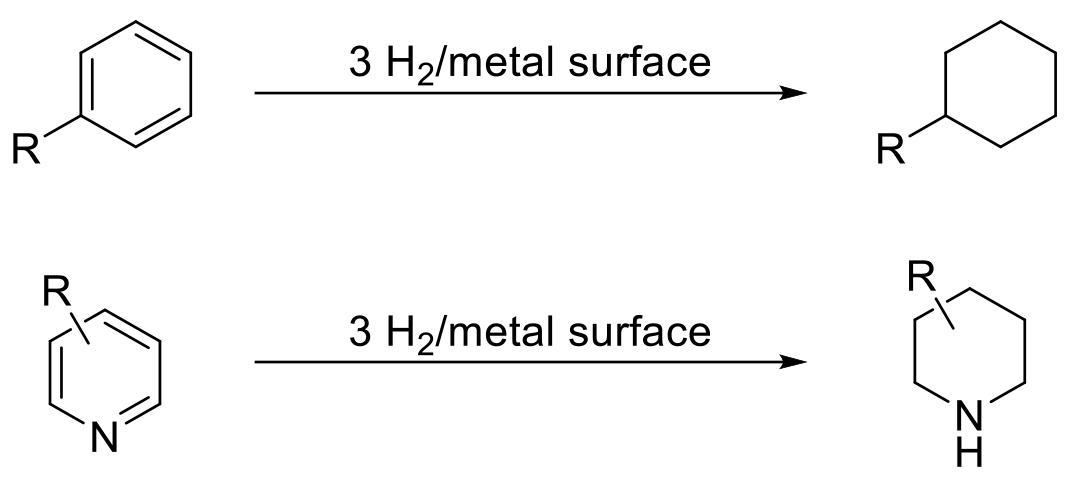
Saturation (or part saturation) of arenes or heteroarenes to cyclohexanes or piperidine-type heterocycles using H2 and a heterogeneous catalyst.
General comments
A common route to substituted cyclohexanes and piperidine–like heterocycles is through heterogeneous catalytic hydrogenation of benzenes and aromatic heterocycles such as pyridines and pyrazines. This strategy allows the use of aromatic chemistry to assemble poly-substituted ring systems prior to hydrogenation to the desired saturated molecule. With heteroaromatics, it is possible to sequentially reduce the double bonds present enabling unsaturation to be retained in the final molecule. With careful choice of catalyst and reaction conditions it is also possible to saturate one aromatic ring in preference to another in the same structure. Both precious metal and base metals (for example Ni) have been employed as heterogeneous catalysts for ring saturation. Several reports claim that homogeneous metal complexes can also take part in achiral hydrogenation of aromatic rings, but the likely active catalytic species here are metal nanoparticles formed in situ.
Key references
Newham, J. The Catalytic >Hydrogenolysis of Small Carbon Rings. Chem. Rev. 1963, 63 (2), 123–137.
Freifelder, M. Hydrogenation of Pyridines and Quinolines. Adv. Catal. 1963, 14, 203–253.
Relevant scale up examples
Hansen, K. B.; Balsells, J.; Dreher, S.; Hsiao, Y.; Kubryk, M.; Palucki, M.; Rivera, N.; Steinhuebel, D.; Armstrong, J. D.; Askin, D.; Grabowski, E. J. J. First Generation Process for the Preparation of the DPP-IV Inhibitor Sitagliptin. Org. Process Res. Dev. 2005, 9 (5), 634–639.
Green Review – Precious Metal Catalyst (PMC) and Base Metal (BM) Hydrogenation
-
Atom efficiency (by-products, molecular weight)
With optimized catalytic efficiency, PMC/BM hydrogenation represents an atom efficient process generating only water and/or low MW by-products. - Safety Concerns
Hydrogenation is a hazardous operation with the gas being highly flammable and capable of forming explosive mixtures with air. Catalytic transfer hydrogenation may avoid the need to handle H2 gas, but it is important to note that many of these reactions generate H2 in situ. Reduction of nitrobenzenes/alkynes/alkenes can be exothermic. Dry PMC and BM hydrogenation catalysts can be pyrophoric and are usually handled water-wet. Mixtures of solvent and catalyst in the presence of air can ignite. Appropriate care needs to be taken after processing in handling the spent-catalyst, which can often be recycled. Some Pt salts used as catalyst precursors are strong sensitizers while some Ni2+ salts are carcinogenic and are likely to be regulated under legislations such as REACH. - Toxicity and environmental/aquatic impact
The chief concern herein is around solubilization and loss of precious metal/heavy metal catalysts into waste streams given that most PMC/BM levels are tightly regulated. The same applies to potential carry through into the final API (updated ICH guidelines for metal residues in APIs – hyperlink to final slide). Some Ni salts are sensitizers and carcinogens and are listed on the EU SVAH list – echa.europa.eu/candidate-list-table (accessed August 30th, 2021) though this is of lesser concern for metallic hydrogenation catalysts. - Cost, availability & sustainable feedstocks
H2 is cheap, non-polluting and can be produced from renewable resources or through the electrolysis of water. - Sustainable implications
All metals have a high LCA impact from mining and refining operations, so use should be catalytic with efficient recovery and recycle. Pd is most used precious metal for hydrogenolysis and this is rated at high risk of depletion. Platinum group elements (Pt, Ru, Pd, Os, and Ir) are flagged as having a high relative supply risk index value (2015 British Geological Survey Risk list – accessed 30th August 2021). There is no concern for abundant base metals like Ni, Cu, Co and Fe.
Green Review – Transfer Hydrogenation with PMC and Base Metals (BM)
-
Atom efficiency (by-products, molecular weight)
Varies from good to poor depending on both the MW and stoichiometry (excess equivalents) used of the donor that is employed. The by-products are water, the oxidized donor, and related by-products (for example – 2-propanol/acetone, hydrazine/N2, cyclohexene/benzene, formate/CO2 etc). Occasionally large excesses of donors are used due to either generate excess H2 to mitigate against loss, or to increase reaction rate. - Safety Concerns
Caution around the use of pyrophoric metal catalysts as per hydrogenation with H2 gas. In addition, systems often produce H2 gas leading to a potentially flammable atmosphere above the reaction. There are several safety attributes of specific individual donors and the by-products they generate that warrant consideration, for example, hydrazine, boric acid, and benzene are all potential carcinogens while borohydride will generate hydrogen gas upon quenching. Safety data (SDS) on the individual components of a proposed hydrogen transfer reaction should be inspected prior to carrying out the reaction. - Toxicity and environmental/aquatic impact
Generally good – ammonia and phosphate may cause issues with discharge into water while higher MW terpenes and siloxanes may bioaccumulate. - Cost, availability & sustainable feedstocks
Most H2 donor molecules are readily available and cheap. In addition, several H2 donors can be obtained from sustainable/biorenewable sources (2-propanol, formate, terpenes). - Sustainable implications
All metals have a high LCA impact from mining and refining operations, so use should be catalytic with efficient recovery and recycle. Pd is most used precious metal for hydrogenolysis and this is rated at high risk of depletion. Platinum group elements (Pt, Ru, Pd, Os, and Ir) are flagged as having a high relative supply risk index value (2015 British Geological Survey Risk list – accessed 30th August 2021).