Acids
Mechanism + Description
Acid-catalyzed deprotection follows protonation followed by fragmentation to the amine, CO2 and a transient t-Bu+ cation which can form isobutylene or react with any nucleophilic species present. Isobutylene is off gassed or under the acidic conditions, can oligomerise. The released amine is protonated, so typically the acid needs to be used in greater than stoichiometric amounts.
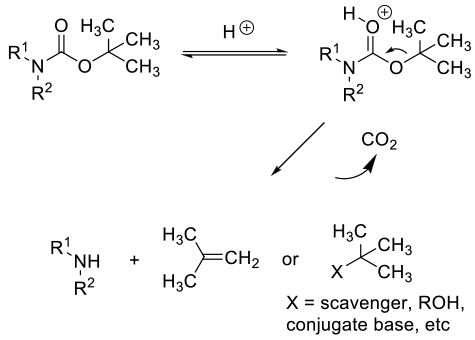
General comments
Most strong acids have been employed for BOC deprotection – typically in organic solvents or solvent- water mixtures.
Typical inorganic acids are HCl, H3PO4 and organic acids are CF3CO2H, Methanesulphonic acid and p-Tosic acid. Acids can be added in anhydrous or aqueous solutions or in the case of HCl, gassed in. Anhydrous HCl is often generated by adding reagents like acetyl chloride or Me3SiCl to alcohol solvents. Traditionally, trifluoroacetic acid (TFA) has been the reagent of choice, but due to its toxic & corrosive properties and environmental persistence -it has largely been replaced by greener materials in larger scale processing. BOC deprotection can be carried out in a range of solvents – see examples. Generally the reaction is scalable – initial exotherms and gas evolution are the biggest hazards associated with BOC removal. The reaction generates isobutylene as a by-product and this can generate safety and emission issues which need appropriate control and handling measures.
Key references
Org. Lett., 2004, 6, 213-215 – deprotection with TFA in dichloromethane
Int. J. Peptide Protein Res. 1993, 41, 522-527 Comparison of 55% TFA/CH2Cl2 and 100% TFA for Boc group removal during solid-phase peptide synthesis
J. Org. Chem., 2006, 71, 9045-9050 – deprotection with H3PO4
Org. Process Res. Dev. 2004, 8, 781-787 – deprotection with MeSO3H in MeOH ‘
Org. Process Res. Dev. 2014, 18, 239−245 deprotection with H2SO4 in toluene
Org. Process Res. Dev. 2014, 18, 969−975 deprotection with HCl in MeCN
Org. Process Res. Dev. 2012, 16, 605−611 deprotection with HCl in THF
Org. Process Res. Dev. 2012, 16, 1069−1081 deprotection with HCl in EtOH
Org. Process Res. Dev. 2010, 14, 1248–1253 deprotection with HCl in EtOAc
Org. Process Res. Dev. 2004, 8, 330-340 deprotection with HCl in toluene
Org. Process Res. Dev. 2014, 18, 215−227 deprotection with MeSO3H in o-xylene
Org. Process Res. Dev. 2011, 15, 367–375 deprotection with MeSO3H in THF
Org. Process Res. Dev. 2008, 12, 877–883 deprotection with Acetyl chloride in EtOAc/EtOH
Org. Process Res. Dev. 2011, 15, 367–375 deprotection with MeSO3H in THF
Org. Process Res. Dev. 2008, 12, 202–212 deprotection with HCl in IPA
Org. Process Res. Dev. 2014, 18, 402−409 deprotection in a multi-phase flow system
Isobutylene / t-Bu+ Sequestration:
BOC deprotection with acidic reagents will generate isobutylene via t-Bu+. It may be necessary to scrub isobutylene from the reaction off-gas to limit releases, or reduce the maximum rate of emission. This can be done by using appropriate acids in scrubber systems to remove isobutylene once formed. The addition of reagents/scavengers to rapidly react with t-Bu+ to produce non-volatile by products is another strategy. t-Bu+ scavenging may also be employed where alkylation is an undesirable side reaction, or PGI’s like t-BuCl might form at unacceptable levels. A number of different reagents typified by thiophenol, thiocresol, cresol, dimethoxybenzene, dimethyl sulfide and other non-volatile sulphides have been used. Often cocktails of these reagents are employed. It needs to be borne in mind that many scavengers are added at greater than stoichiometric amounts and thus can adversely affect mass efficiency and give additional handling issues.
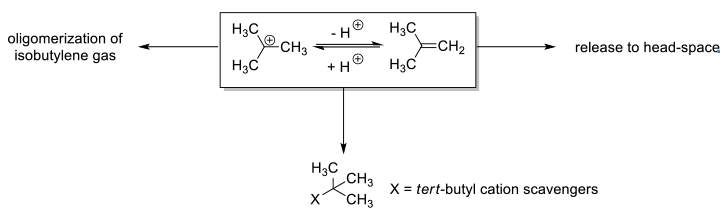
- Isobutylene Overview
- Physical Properties:
- Colorless gas
- Boiling Point = -7.0 °C
- Hazard Identification:
- Flammable – forms explosive mixtures with air/oxidizing agents
- Potential Health Effects:
- Mucous membrane irritation; drowsiness; headache
- Physical Properties:
Potential issues with isobutylene emissions are maximized if reactions are run cryogenically then rapidly warmed during work-up.
Org. Process Res. Dev. 2009,13, 1169–1176 Controlling the rate of isobutylene emission
Org. Process Res. Dev. 2005, 9, 39-44 Minimizing Isobutylene Emissions from Large Scale tert-ButoxycarbonylDeprotections
Int. J. Peptide Protein Res. 2009, 36, 255-266 A cleavage method which minimizes side reactions following Fmoc solid phase peptide synthesis
Int. J. Peptide Protein Res. 1984, 23, 565-572 Improved selectivity in the removal of the tert-butyloxycarbonyl group
Bull. Chem. Soc. Jpn. 1980, 53, 464-468 The Modification of Tryptophyl Residues during the Acidolytic Cleavage of Boc-groups. I. Studies with Boc-Tryptophan
J. Peptide Sci. 2006; 12: 227–232 terminal N-alkylated peptide amides resulting from the linker decomposition of the rink amide resin. A new cleavage mixture prevents their formation
Protein and Peptide Letters 2002, 9(5), 379-385 – The use of 3,6-dioxa-1,8-octanedithiol (DODT )as a non-malodorous scavenger in Fmoc-based peptide synthesis
Relevant scale up example
Experimental
25 kg scale
Org. Process Res. Dev. 2005, 9, 466-471
Experimental
1 kg scale
Org. Process Res. Dev. 2014, 18, 665−667
Experimental
20 kg scale
Org. Process Res. Dev. 2005, 9, 499-507
Experimental
40 kg scale
Org. Process Res. Dev. 2009, 13, 1145–1155
Experimental
1 kg scale
Org. Process Res. Dev. 2006, 10, 339-345
Experimental
110 kg scale
Org. Process Res. Dev. 2009, 13, 900–906
Experimental
136 kg scale
Org. Process Res. Dev. 2011, 15, 503–514
Experimental
136 kg scale
Org. Process Res. Dev. 2000, 4, 526-529
Experimental
32 kg scale
Org. Process Res. Dev. 2011, 15, 1018–1026
Experimental
800 g scale
Org. Process Res. Dev. 2011, 15, 831–840
Experimental
100 kg scale
Org. Process Res. Dev. 2005, 9, 440-450
Experimental
35 kg scale
Org. Process Res. Dev. 2004, 8, 945-947
Green Review
-
Atom efficiency (by-products Mwt)
Dependent on the acid used – most are employed in large excess. The chosen acid should ideally have a low Mwt and be employed in as close to stoichiometric quantities as needed for acceptable reaction rate. Overall, HCl, H2SO4 or H3PO4 are preferred acids.
Atom Efficiency (By-Products Mwt < 200 g/mole):- HCl By-Products (assuming 1 equiv of acid) = CO2 (44.0 g/mole) + isobutylene (56.0 g/mol) + HCl (36.5 g/mole) = 136.5 g/mole
- MSA By-Products (assuming 1 equiv of acid) = CO2 (44.0 g/mole) + isobutylene (56.0 g/mol) + MSA (96.1 g/mole) = 196.1 g/mole
- Phosphoric Acid By-Products (assuming 1 equiv of acid) = CO2 (44.0 g/mole) + isobutylene (56.0 g/mol) + Phosphoric Acid (98.0 g/mole) = 198.0 g/mole
- p-TsOH By-Products (assuming 1 equiv of acid) = CO2 (44.0 g/mole) + isobutylene (56.0 g/mol) + p-TsOH (172.1 g/mole, anhydrous) = 272.1 g/mole
- Safety Concerns
Main issues are around corrosion and handling of strong acids. CF3CO2H is highly corrosive and volatile and should be avoided. Acid deprotection of BOC will give rise to isobutylene – see appropriate section of guide. Consideration should be given to the generation of potential PGI’s. - Toxicity and environmental/aquatic impact
Most mineral acids pose little problem after neutralization and dilution. High phosphate levels may be regulated due to concerns over eutrophication. Organic fluorinated sulfonated acids and other fluorinated materials (trifluoroacetate) can be persistent and accumulative in the environment. Methanesulfonic and p-toluenesulfonic acids are biodegradable. - Cost, availability & sustainable feedstocks
Very cheap and readily available, although sulfonated organic acids are prepared from petrochemical sources. Some organosulfonates are becoming available prepared from bio-renewable sources. - Sustainable implications
Generally good with mineral acids – less so for sulfonate esters and fluorinated acids/sulfonates which will have a bigger LCI in their manufacture and more issues with persistence in the environment when flourinated.